@thesisgems for our next show date
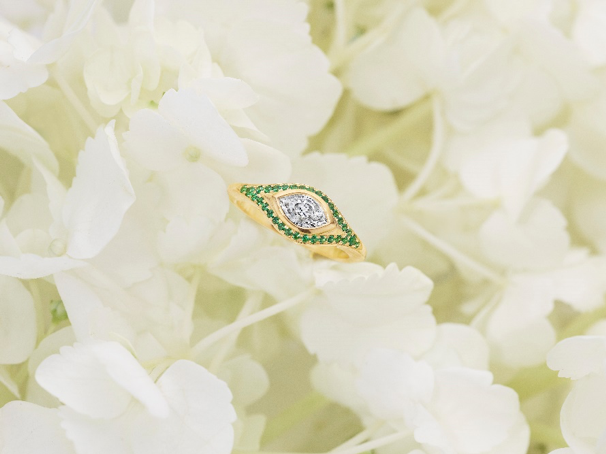
The Art of Gemstone Cutting
Posted on
“How much art and science, and what attention, what care is necessary to render the sun-beams which are imprisoned in a tiny polyhedron of pure carbon, brilliant and sparkling!” — Charles Blanc, Art in Ornament and Dress, 1875
Diamond and gemstone cutting reach back to prehistoric days when humans learned to carve and shape stones using other, harder stones.
From drawings chiseled in cave walls to blades made from sharp flakes of stone, ancient cultures developed the basic techniques that gave rise to modern drilling, tumbling, polishing, and more.
Over the millennia, gemstone cutting has evolved into an intricate artform utilizing advanced technologies. Read on to learn how our artisans free the “sun-beams” from rough stones to create “brilliant and sparkling” jewels.
The Evolution of Lapidary Arts
The art of gem cutting and polishing is called lapidary, and the artist doing the cutting and polishing is also called a lapidary or lapidarist.
The earliest lapidaries pulled stones from the river and contemplated the smoothing effects of erosion. Now they can facet a diamond or cut a cabochon with astonishing accuracy.
For centuries, lapidaries shaped gemstones using slow, arduous processes like bruting: scraping one diamond against another to carve a crude shape.
Today, more precise bruting can be accomplished with lasers and power-driven machines.
Still, the basic techniques are not a far cry from our ancestors hitting one stone against another. Whether she’s using a programmable machine or a simple hammer and muscle, a lapidary understands how to work with each stone based on its unique level of hardness and desired shape.
Gem Cutting Styles and Techniques
Gemstone artists continue to push their craft forward by experimenting with unique cuts and modern techniques. To achieve a variety of gemstone styles, from a classic brilliant cut to a trendy briolette cut, lapidaries rely on the following core processes and techniques.
- Polishing or Tumbling
Just like the rotary rock tumblers people use at home, gemstones are usually first refined by tumbling them in a barrel with various abrasives. The stones are then finely polished by pastes of hard substances.
Diamond, the hardest mineral, is frequently used to polish stones (including diamonds). Man-made polishing compounds, such as silicon carbide and cerium oxide, are also commonly used.
(“Baroque” Mexican fire opal pendant )
- Faceting
Faceting is the process of cutting a gemstone to create the ideal finished design. Through sawing, grinding, and polishing, the lapidary makes a geometric pattern of small planes, or facets, on the stone’s surface.
When cut at the right angles and depth, the facets create a dazzling interplay of light as it passes through the diamond, emerald, or ruby. Faceting today is done using table-top machines that give lapidaries exacting control over every angle.
- Cabochon Cutting or Cabbing
Not all stones are faceted. The cabochon form — relatively flat and rounded on top — is the preferred shape for softer stones that aren’t enhanced by faceting. The best way to show off an opal’s play-of-color, for example, is by polishing a smooth surface to reflect an even band of light.
Cabbing involves twirling the stone to grind and sand progressively smoother curves either by hand or machine.
(Colombian emerald cabochon and fancy cut rhomboid shape diamond ring)
(Botswana rose cut diamond pendant necklace)
Our Jewelry is a Cut Above
The artists at Thesis Gems & Jewelry are influencing the entire gemstone industry by sourcing rough stones from sustainable and socially responsible mining operations.
We work with some of the finest contemporary lapidary artists to shape these ethically-sourced gemstones into true works of art.
Whether it’s a fancy cut diamond ring or an emerald cabochon, every stone we set has been thoughtfully shaped to bring out its best qualities.
Reach out now to find — or custom design — your own perfectly cut and polished wearable masterpiece.
Subscribe to our newsletter
News, Recent Collabs and Events. Directly to your inbox.
Contact
(510) 898-6660